Innovation Award for R&D on Biogas Separation Technology to Bio4Energy Researcher
/in News/by Anna StromA Bio4Energy research leader has been appointed Innovator of the Year by his employer Luleå University of Technology, Sweden, for developing energy-efficient technology for biogas upgrading for use as vehicle fuel.
Professor Jonas Hedlund and his team on Bio4Energy Catalysis and Separation have a history of developing and perfecting membranes from zeolites. The latter are microporous, crystalline aluminosilicate materials commonly used as commercial adsorbents or catalysts.
Carbon dioxide separation from biogas and saltwater purification are two main avenues for use of the membranes that the researchers are developing. To the best of their knowledge, they were the first team to develop large membranes from Chabazite, a so-called tectosilicate mineral of the zeolite group.
What set the effort apart, is the quality of the membranes developed.
Hedlund’s business venture ZeoMem Sweden is the only one to offer membranes for sale that are selective enough and which provide sufficient throughput for them to be used in industry, according to a press release from LTU.
“Zeolite membrane processes are a new, inexpensive and compact technology, which is approximately 90 per cent more energy efficient the technology in use”, Hedlund said;
“We estimate that these processes could be used in five per cent of separation processes worldwide. This means that the potential for energy savings from [using] new zeolite membrane processes is on a par with the annual consumption of [fossil] oil in Sweden”.
The goal is for the new-style zeolite membranes to be produced at an automated factory at Luleå, for ZeoMem Sweden to be able to provide membranes for purification of natural gas or ethene in large-scale industrial operations.
In its award motivation, LTU called the effort “an important contribution to the green transition and a more sustainable world.
“After more than 20 years of research on zeolite membranes, Jonas Hedlund has developed a unique and scalable solution for the purification of biogas”.
Bio4Energy has world-leading scientists on it research platform for Chemical Catalysis and Separation Technologies. Jonas Hedlund, professor at Luleå University of Technology, has been ranked among the top one per cent of leading scientists in chemical technology in a 2021 review by Stanford University, U.S.A.
Plastic Waste, Carbon Nano Materials, Photothermal Imaging in New Research Projects
/in News/by Anna StromBio4Energy researchers have won funds from the Swedish Research Council for multi-annual projects on “upcycling” of plastic waste, evaluation of carbon nano materials for use in electrodes and photothermal imaging of fatty acids and droplets.
The projects and their participants are acknowledged as follows:
- Development of sustainable and efficient processes for upcycling of PET waste into value-added chemicals as building blocks for recyclable materials, Ulrika Rova, Bio4Energy Biochemical Conversion at Luleå University of Technology (LTU). Co-applicants at LTU are Suman Bajracharya, Annie Modestra Jampala and Paul Christakopoulos.
- Experimental and theoretical evaluation of carbon nano materials with hierarchical porous structures and large surface area for use as sustainable electrodes, Kristiina Oksman, Bio4Energy Biochemical Conversion. Collaboration partners are Staffan Lundström and Andreas Larsson. All are affiliated with LTU.
- High-speed mid-infrared photothermal imaging of fatty acids and lipid droplets in living cells, Florian Schmidt, Bio4Energy Thermochemical Conversion at Umeå University.
- Raman spectroscopy applied for neurosurgery – assistance in decision making on tumor boarders and tumor grade, Kerstin Ramser, Bio4Energy Thermochemical Conversion at LTU. Collaboration partners are Karin Wårdell, Jan Hillman, Johan Richter, Martin Hallbeck; all of the University of Linköping; as well as Joel Wahl of LTU.
Young Researcher Wins Prize for Development of Sustainable Artificial Membranes
/in News/by Anna StromHe wants to make environmentally friendly, artificial membranes that mimic the human body’s inbuilt membranes. Like a kidney’s filtering function that, in healthy people, keep functioning through a lifetime, said Naser Tavajohi, assistant professor at Umeå University.
He is one of Bio4Energy’s up-and-coming young researchers, who has just walked the red carpet for having won a prize from the Royal Swedish Academy Skytteanska Samfundet. It is one of 18 Royal Academies in Sweden.
“I have a dream to be a world-leading scientist in my field, who solves the life problems. I love what I am doing”, Tavajohi said in an online interview.
Membrane technology is part of many industrial applications, but they are not necessarily free of negative impacts on the natural environment, he explained;
“We want to make sustainable membranes for ‘green’ and ‘blue’ energy.”
Tavajohi’s group in Bio4Energy Chemical Catalysis and Separation Technologies focuses on making polymeric membranes from bio-based materials or solvents.
Wastewater treatment, energy storage, gas separation and a possible ‘brine refinery’ are target areas for the type of membranes that they have in mind.
The membranes “should be of superior, long-term function. We are trying to mimic biological, smart, stable, long-life membranes”, said the ambitious technology researcher.
In terms of large-scale research and development projects, Tavajohi and group members are part of Swedish national project to create a biorefinery for organic waste.
In the Bio4Energy research environment, they give input to a current project designed to make liquids for carbon dioxide separation from other gases, as well as a past one on bio ethylene purification using energy-efficient technology.
Bio4Energy Researcher Awarded Medal for ‘Exceptional Contribution’
/in News/by Anna StromBio4Energy researcher Rosario García-Gil has been awarded a prize for “exemplary and exceptional contribution of lasting value” for her work as a plant scientist and a research leader at the Swedish University of Agricultural Sciences (SLU) at Umeå, Sweden. It comes in the form of a gold medal.
“Right from the start Rosario García-Gil focused on research that can benefit the world around us. Much of it is about tree breeding for increased wood production. She also treats issues of ecology and sustainability. She has built a large number of collaborations to reach her goals”, according to a press release from the SLU.
Surprised but seemingly delighted, assistant professor García-Gil replied to an e-mail invitation from Bio4Energy Communications.
“This is… totally unexpected”, she wrote, “but you know, working with excellent people brings the best of you”.
Biologist García-Gil trained at the University of Valencia in Spain and served as a researcher at the University of Uleåborg, Finland; before taking up her role at SLU and Umeå Plant Science Centre in 2005.
Among research efforts with Bio4Energy, the co-coordination of two large projects stands out. Whereas one is a multinational project on the integration of UN Sustainable Development Goals in Forest Management, the other aims to integrate the concept of remote sensing in studies that draw on forest genetics. The aim of the latter is to adapt forest management practises to altered conditions brought about by a changing climate.
In terms of collaboration with other members of the Bio4Energy research environment, García-Gil and her team are part of projects on the effect of drought on spruce wood chemistry and feedstock use, as well as detecting and quantifying resin canals in spruce.
Polymer Lignin May Be Modified for Drought Resistance in Plants
/in News/by Anna StromBio4Energy Associated Member Edouard Pesquet, previously with Umeå University, is part of a group of internationally leading scientists on fundamental research on the plant polymer lignin. Pesquet was part of the organisation team that started the international conference Lignin in 2014. Because of his experience with Bio4Energy at Umeå, Sweden and the support he gained during his time here—becoming a Gunnar Öquist Fellow—Pesquet has continued being part of, and publishing with, the Bio4Energy Research Environment.
Stockholm, 22 September 2022
A new study shows that we can create and select plants that can better recover from drought without affecting the size of the plant or seed yield, by genetically modifying their lignin chemistry. These results could be used in both agriculture and forestry to tackle future climatic challenges.
Lignin, the second most abundant biopolymer on Earth, represents about 30 percent of the total carbon on the planet. It allows plants to conduct water and stand up right; without lignin, plants cannot grow nor survive.
For long, scientists did not consider that lignin had a “code” like in DNA or proteins. Researchers led by Stockholm University, Department of Ecology, Environment and Plant Sciences (DEEP), in collaboration with Stockholm University Department of Material Sciences (MMK) and Tokyo University of Agriculture and Technology (TUAT); have now challenged this old paradigm by demonstrating the existence of a lignin chemical “code”.
They showed that each cell uses this code to adjust their lignin to function at its optimum and resist stresses. These results are published in the high-ranking scientific journal The Plant Cell and could be used in both agriculture and forestry to tackle future climatic challenges.
“It takes only one simple chemical change, just one hydrogen atom apart from alcohol to aldehyde to make plants highly resilient to drought in conditions where alcohol-rich plants would all die”, explained Edouard Pesquet, associated professor in molecular plant physiology and senior author of the study.
Interestingly, professor Shinya Kajita from TUAT showed that such large increases of lignin aldehydes can occur naturally in the wild. In the Japanese silk industry for example, mulberry with high lignin aldehyde levels have long been used and loved by silk caterpillars.
“These results [not only] revise our understanding of lignin and plant water conduction, but also open great possibilities to use the lignin ‘code’ to improve crops and trees to face water availability problems. The modification of lignin chemistry at the single cell level, is ultimately the mechanism enabling plants to grow, hydrate and resist climate change stresses”, Pesquet said.
Text by Amanda Gonzalez Bengtsson, with editing by Anna Strom
Contacts
Edouard Pesquet, Stockholm University — Bio4Energy Associated Member, formerly with Bio4Energy at Umeå University and Umeå Plant Science Centre
Aji Mathew, Stockholm University — Formerly with Bio4Energy at Luleå University of Technology
Scientific articles
Plant biomechanics and resilience to environmental changes are controlled by specific lignin chemistries in each vascular cell type and morphotype, by Ménard, Blaschek et al. is published in the journal The Plant Cell September 2022.
RISE to Invest SEK350 Million in Its Biorefinery Test Bed Environments
/in News/by Anna StromBio4Energy partner RISE Research Institutes of Sweden have committed to an investment of SEK350 million in the “coming years” to expand their test bed environments at Piteå and elsewhere in Sweden.
“In the coming years, we at RISE will make an additional investment of 350 million kronor to strengthen our range of test beds in biorefinery and establish a world-class centre for upscaling of processes pertaining to a circular bioeconomy”, said Magnus Hallberg, head of division at RISE Bioeconomy and Health, in a press release.
Elisabeth Wetterlund, Bio4Energy deputy programme manager, attended the inauguration ceremony 15 September.
“This [expansion] will open the door to more exciting strategic collaborations between RISE Piteå and several of the Bio4Energy platforms, so that we can develop even further our knowledge about processing and upgrading of different types of residual streams to renewable fuels, materials and chemicals”, according to Wetterlund, professor at Luleå University of Technology.
“The new and expanded ted bed activities at RISE are incredibly important to the development, upscaling and industrialisation of different biorefinery processes—for Bio4Energy and for Sweden at large”, she said.
IEA: Bioenergy Part of Sustainable Energy Mix
/in News/by Anna StromBio4Energy highlights a September 2022 press release by the International Energy Agency’s Bioenergy branch (IEA Bioenergy). The press release aims to dispel “misconceptions and misrepresentations” in relation to use of low-quality forest biomass for energy purposes. The press release may be found here, Facts, not fiction: Bioenergy from wood contributes to Europe’s energy security and is part of a sustainable energy mix.
Summer Greetings from Bio4Energy
/in News/by Anna StromIt is the time of the year when we allow ourselves to take a break, to come back in autumn with sunshine and blue skies behind our eyelids; ready to tackle a new semester of making tools and methods for producing biofuels, “green” chemicals and bio-based materials.
Before we go, we want to wish you all the best. Thank you for following us. We hope to continue the cooperation or collaboration with you from September.
Would you be interested in receiving our news? Sign up for the Bio4Energy Newsletter, in the right-hand column of this page.
Current issues as follows: In English, Biocarbon to Replace Fossil Coal in Sweden’s Iron, Steel Industries & Reuse of Waste (mailchi.mp) and in Swedish, Biokol kan ersätta fossilt kol i svensk järn- och stålindustri (mailchi.mp)
Stay in touch!
2021 Bio4Energy Annual Report Is Out
/in News/by Anna StromThis is the release of the Bio4Energy Annual Report for 2021.
It gives an overview of the research and development conducted on the seven Bio4Energy Research and Development Platforms.
It hints at the work of the Bio4Energy PhD students, by listing the topics for and names of those who successfully defended their thesis, at the end of their PhD project.
It shows which research teams won a special acknowledgement, in the section for Awards and Commissions of Trust.
There is a section for Media and Outreach.
Last but not least, the Bio4Energy Advisory Board is profiled. It is made up of key people for the bio-based sector in Sweden. It serves to guide the Bio4Energy Board and programme managers, in their efforts to make the research environment useful not only to itself, but also to the sector.
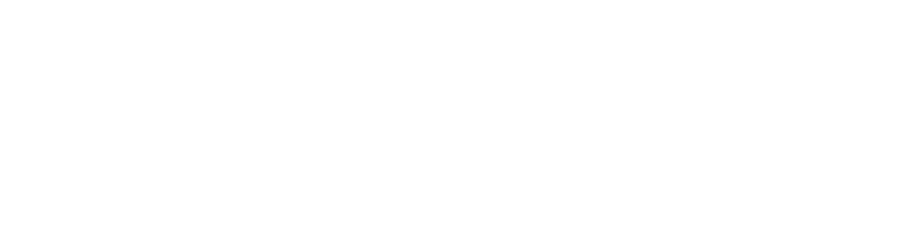
VISITING ADDRESS
ADDRESS
Bio4Energy
Umeå University
SE-90187 UMEÅ
Sweden